CASE STUDY
EAST COAST ORGANICS
How a thriving farm produce delivery operation has benefited from electrified vans…
Launched in 1996, East Coast Organics operates a thriving farm produce delivery scheme from its headquarters just outside Edinburgh, with sustainability at its core. In 2015, the company embarked on the first electrification of its small van fleet and, for managing director, Mike Callender, it met a long-term goal.
“The main factor that made electric vans feasible for us was the availability of rapid chargers,” he explains. “As we are 15 miles out of town, few of our delivery runs are possible without a top-up charge. In general the drivers prefer the electric vans, though winter range can be challenging.”
The fleet comprises three Nissan e-NV200 vans, two of which were purchased new using interest-free loans from the Energy Saving Trust, and the third was nearly new.
All are versions with a 24kWh battery, equipped with DC rapid charging, and fitted with bespoke graphics over eye-catching canary yellow paint, helping to raise awareness locally.
Duty cycles are demanding. Each van does around 100 drops per day, five days per week, which Callender says saves £5,000 in fuel costs per vehicle, per year, compared to their diesel predecessors, while also spending less time off the road for maintenance. Efficient deliveries are assisted by the company’s ‘Boxmaster’ routing software, developed in-house and now offered to other fleets. Built because a suitable off-the-shelf solution didn’t exist beforehand, this plots customer requests as part of a delivery route, and organises billing too.
“The main factor that made electric vans feasible for us was the availability of rapid chargers.”
Mike Callender – managing director, East Coast Organics
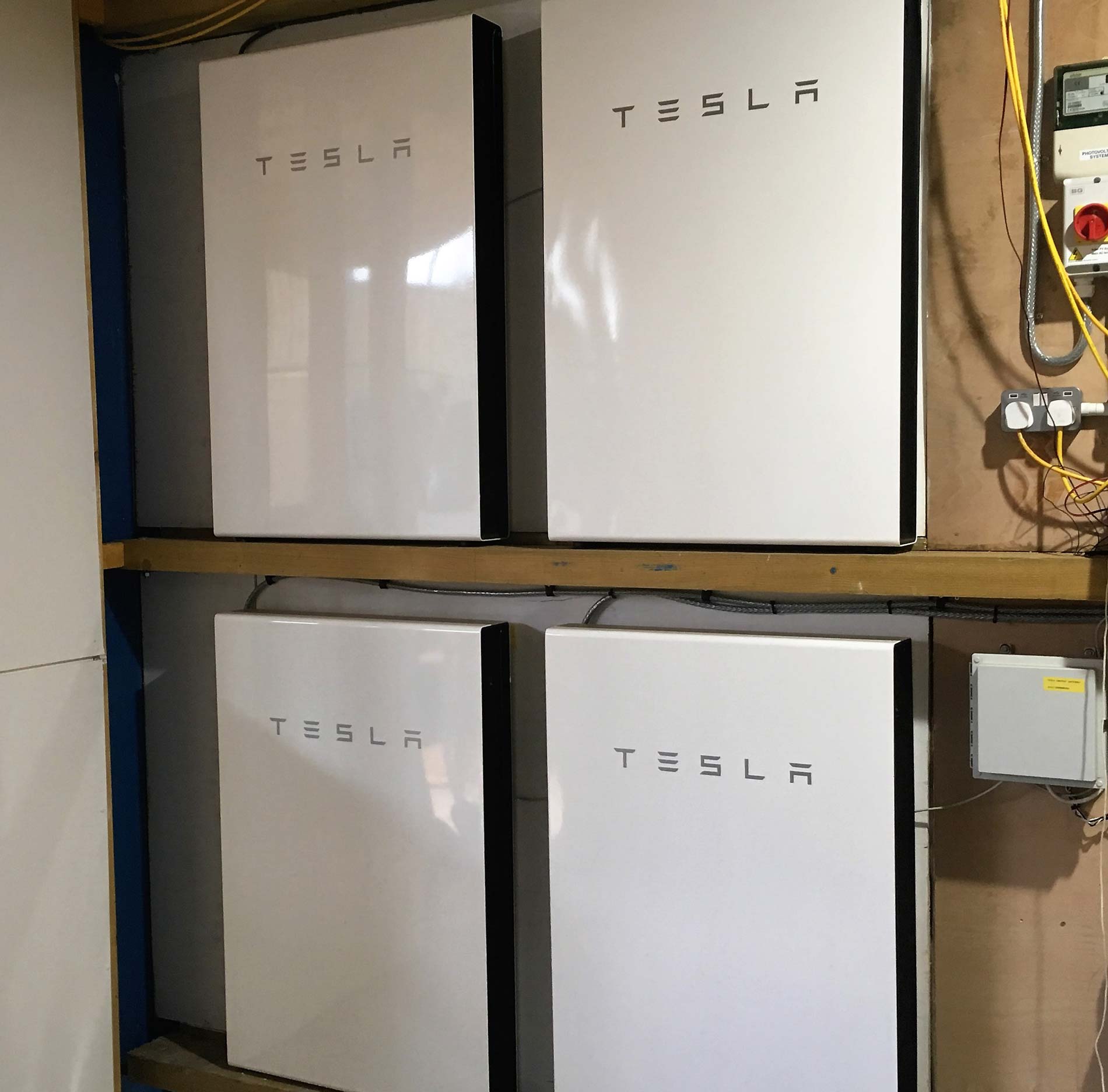
However, the newcomers have required adaptations elsewhere. The e-NV200 is marginally smaller than would be ideal, so the vans utilise a bespoke delivery box designed to fit the load area, which can also be flattened and returned for reuse. Further efficiencies here are an ongoing area of focus for the company.
“The biggest challenge these days is avoiding plastic, which is possible but expensive,” continues Callender. “We are about to trial a new clear compostable bag, which we are having manufactured here in the UK.”
Relocating to a bespoke production hub last year has introduced new efficiencies. The building features a 26kW solar array, with four Tesla Powerwall energy storage units in the workshop. These are used to trickle-charge the vans overnight, and the site also generates enough energy to feed some back to the grid during the summer.
Staff are offered discounts on bikes to cycle to work, and rotate between working on the farm, in the office and driving the vans.
The company’s electrification programme won the Electric Vehicle Hero title at the 2019 Energy Saving Trust Fleet Hero Awards, and work is underway on the next phase. As with the first vans, it’s reliant on new product. Larger-capacity vans will enable the rest of the fleet to switch too.
“The small size of the vans means we have to top them up with more boxes during the day on some runs,” says Callender. “This is done with a diesel van and the solution is not ideal. The option has always been to wait for larger affordable electric vans to be produced, several are coming out this year, or to lease property in the city for a depot and have our own rapid charger.”
